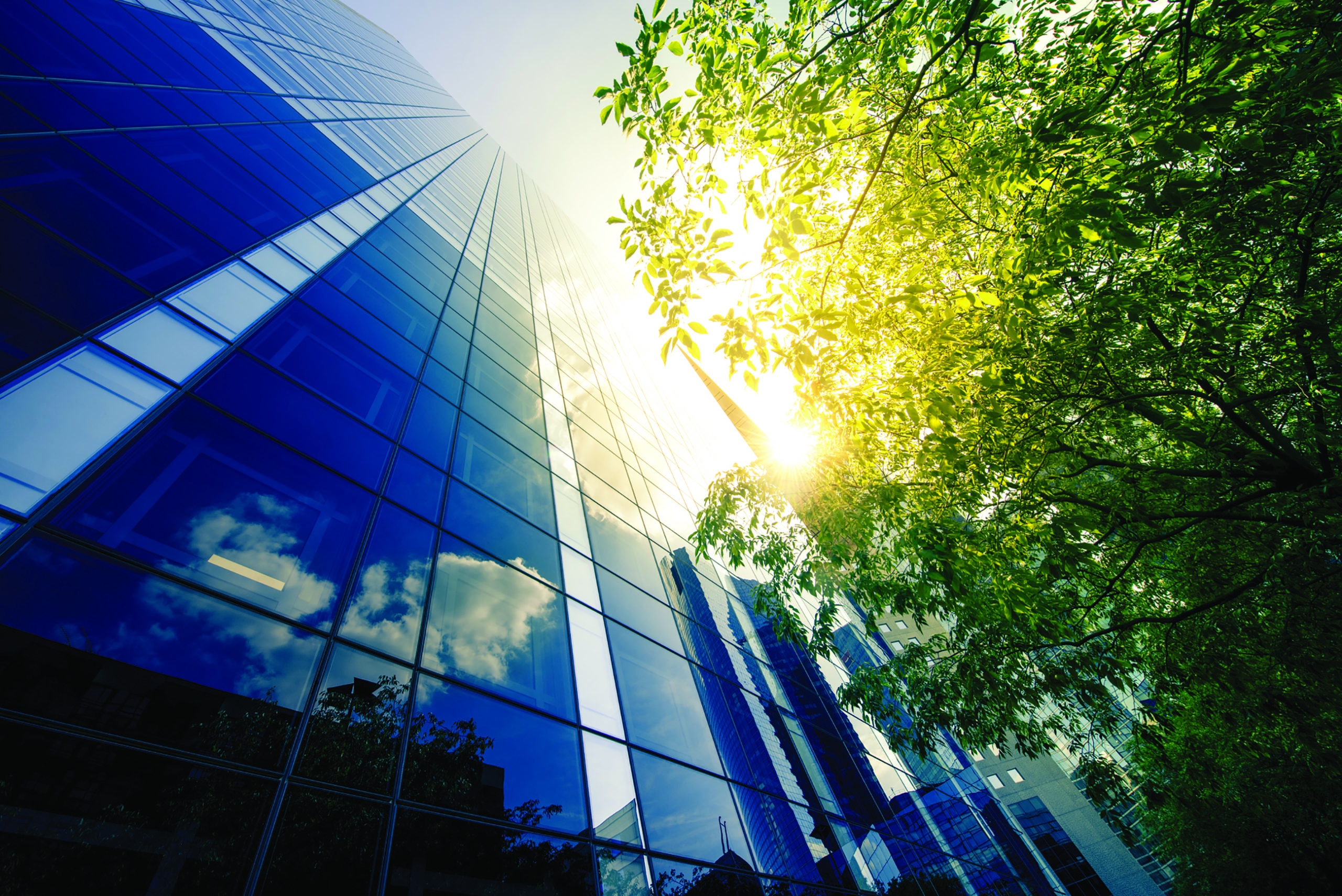
With COP26 taking place this November all eyes are on sustainability in the built environment. For ironmongerers this means being increasingly asked about product lifecycle. Karen Trigg reports.
In recent times, the quest for environmental sustainability has become more widespread. A 2019 survey found that 47% of internet users worldwide had stopped consuming products and services that opposed their personal values – protecting the environment topped the list as a reason for switching that product or service. With the expectations on corporate responsibility also growing, it’s clear that meeting environmental obligations – whether as an individual or organisation – is growing in importance.
For ironmongery, this is no different. Building environments account for around 40% of the UK’s carbon footprint, and the products used within are contributing to this total. With this in mind, it’s critical for those in ironmongery to understand their impact on the planet and consider changes that meet environmental conventions and key sustainability principles.
Environmental impact
The construction industry, in general, produces a staggering amount of waste. According to the 2018 edition of UK statistics on Waste, in 2014, the UK generated a total of 202.8 million tons of waste, with construction, demolition and excavation responsible for 59% of that, totalling 119.6 million tonnes.
What’s more, the construction industry also accounts for 55% of material consumption in the UK. Conceivably, ironmongery is a vital part of the fabric of a building.
With architectural ironmongery constructed of iron, steel, aluminium and timber, this subset of the construction industry would also have an impact on the environment and contribute to these statistics.
To combat this, as cited in the ‘GAI Specifiers Guide to Ironmongery and the Impact of the Environment’, decision makers can look to ‘reduce, reuse and recycle’ in a bid to improve their sustainability efforts. Much of this is being done by eliminating product and packaging waste, repurposing excess or discarded materials and creating innovative products and solutions that are better placed to meet environmental regulations.
Hardware’s carbon footprint
From using green energy to passive heating and cooling, there are numerous focus points to consider when looking to meet carbon neutrality or, better still, become carbon negative in a building environment. Though, to improve things further, decision makers must focus on extending the product life cycle of architectural ironmongery, suggests Sue Corrick, product marketing manager at Allegion UK.
By extending the life cycle of ironmongery and minimising the need for repeat manufacturing, shipments and packaging, manufacturers can further reduce carbon footprint and protect our future environments"
Sue Corrick, product marketing manager at Allegion UK.
“By extending the life cycle of ironmongery and minimising the need for repeat manufacturing, shipments and packaging, manufacturers can further reduce carbon footprint and protect our future environments.
“At a basic level, there are numerous stages that describe a product’s life cycle, all of which can have an impact on the environment, whether at the material extraction, manufacturing or construction stage. However, the life cycle of a construction product may also go through maintenance, refurbishment and demolition stages – of which, longevity and recycling elements must be considered to ensure the hardware outlasts the building structure itself.
“Take product packaging for example. With the impending Plastic Packaging Tax and practices such as the Extended Producer Responsibility (EPR) coming into effect in 2022 and 2023 respectively, the onus is now on manufacturers to review and seek plastic and polystyrene alternatives before implementing plans that make use of renewable resources and 100 percent recyclable materials. We’ve been making those steps at Allegion UK, right down to label classifications (such as FSC certifications) but with various stages of the product life cycle to consider, our collective efforts can’t end there.
“Innovation aside, manufacturers must also adhere to the correct standards, as has always been the case. With construction at the heart of waste in the UK, there has been an increased demand for information on the environmental impact that construction products have, and with that we’ve seen a rise in institutes and initiatives that can now help manufacturers provide that necessary product transparency.
“ISO 14001 for example, is the most recognised international standard for environmental management systems and is designed to improve resource management and overall environmental performance throught the product life cycle. By following this standard – of which is compatible with other recognised standards – manufacturers can better their environmental standing and take the first step in providing visible and detailed evidence for consumers that now seek this as part of their purchasing decision.
“Decision makers can also choose to enrol in further programmes that focus on sustainability. One of which is the Environmental Product Declaration (EPD), a complete mapping of a product’s environmental footprint and a standardised way to communicate the environmental impact of a product. An EPD reports on the environmental data of your product – everything from material acquisition to waste generation – and in accordance with the international standard ISO 14025, now sets the benchmarks that products should meet. For an EPD to be awarded, a Life Cycle Assessment (LCA) must also be undertaken on a product and this must meet Product Category Rules (PCR) to be issued an EPD, and therefore be declared as acceptable in building rating schemes such as BREEAM.
“We’re honoured to be part of the EPD programme at Allegion UK, and although it’s not currently mandatory for manufacturers in the UK, we urge others to consider the importance of EPDs in ironmongery.
The significance of sustainability is growing quickly, and by stepping up, decision makers can continue raising standards across all areas of the product life cycle, from manufacturing to recycling, and thus create better building environments for the future.”
Karen Trigg is business development manager south east at Allegion UK.