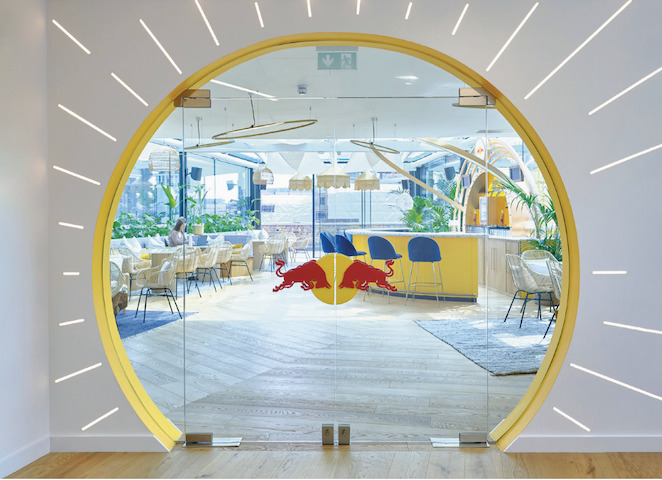
AC Leigh was briefed to produce a bespoke bar feature door handle for Red Bull HQ in London, styled on the iconic logo and making use of the well-recognised colour palette of Red Bull.
AC Leigh developed an initial concept sketch of a handle, showing the two Red Bull bulls welcoming you to the area with the traditional yellow sun completing the handle. It asked Instinct Hardware to make this reality.
Instinct’s design team created a working CAD design of the logo and the handle using Solidworks design technology. These photo-realistic renders were sent through to AC Leigh for approval.
Initially, concerns were raised about how the handles would interact on the face of the door when this was swung open. Instinct was able, thanks to the design technology capabilities, to show that the handles would cause no interference when placed on the door. Advanced rendering and digital illustration allowed Instinct to demonstrate the door opening and closing and where the handle points would meet and close.
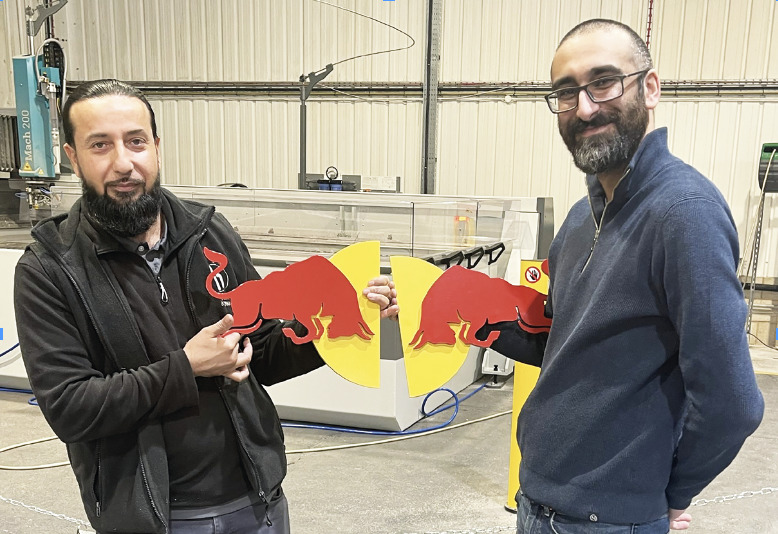
The client required specialist RAL powder coated colours for the finished item, so sample swatches were provided (on the correct material) within seven days for approval. This was done alongside the manufacture of the handles, so not to slow down the production times.
Delivery was required within six weeks of the order so the process was managed in-house, to minimise delays. The approved designs were turned into technical drawings, to provide works instructions for the manufacturing team. The CAD files were converted to DXF in Solidworks and these were then imported into FlowXpert to generate the program for the waterjet, meaning full use of in-house integrated CAM systems.
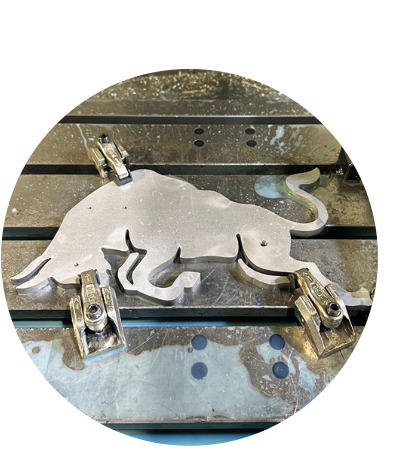
Instinct’s waterjet cutting machine provided the ideal tool for this level of intricate cut, effortlessly slicing 10mm thick solid marine-grade 316 stainless steel. Using the waterjet meant that the intricate edges needed for the outline of the bull were precisely cut. Lasers have previously been used for this kind of work but waterjet provides cleaner edges – meaning no additional time-consuming hand filing is required for buffing.
Thread milling for tolerance
The components were then clamped to the CNC vertical machining centre to ensure the fixing holes were made to the tightest tolerance. Due to the slim 10mm material used, the decision was made to thread mill the required holes rather than the traditional drilling and tapping techniques. Thread milling has the advantage of milling holes to the perfect depth and tolerance, by using a specialist Vargus solid carbide tool. This small thread mill packs the punch needed to work with solid steel and once again just adds to the strength and clean finish of the handle.
The corner edges of the handle were hand-finished and smoothed and the handle then had the specified RAL powder-coated colours applied, to completely match with the branding and the surroundings in which it was to be placed. Hand inspected, hand-assembled and then securely packaged, the pull handle made its way to the HQ within the six week deadline.