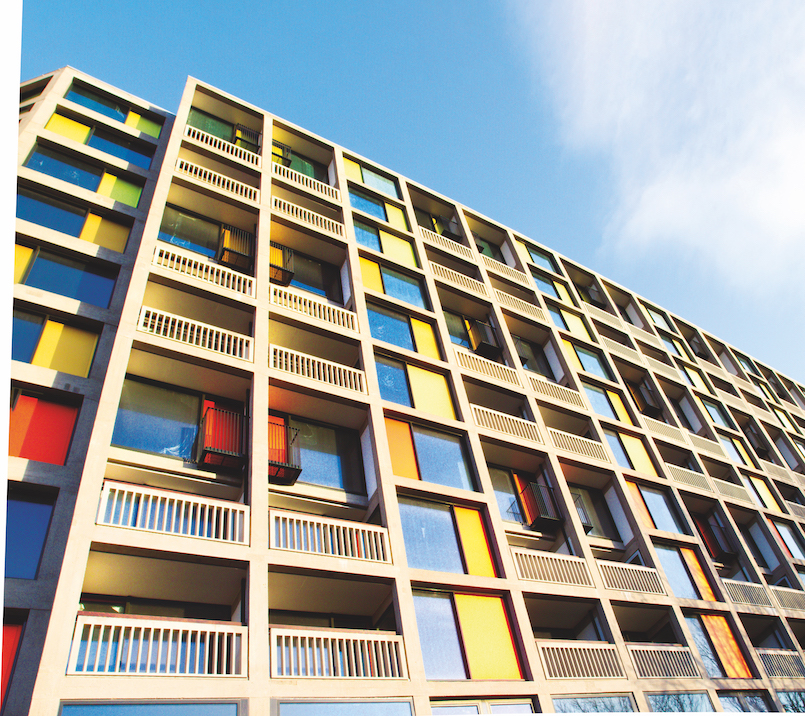
“The greenest building is the one that already exists”. When Carl Elefante,
former president of the American Institute of Architects, said this in 2007 he was
making the case for reusing and upgrading existing buildings, rather than demolishing and replacing them.
There is increasing clamour for retrofitting to replace razing in a bid to meet net zero targets, preserve heritage buildings and manage waste caused by construction. The statistics back up this argument. Retrofitting an existing building can typically save between 30% to 50% of the costs compared to constructing a new building. 50,000 buildings are demolished every year in the UK and when looking at the whole-life carbon impact of buildings the Royal Institution of Chartered Surveyors (RICS) has found that, by practical completion stage, 35 per cent of the whole-life carbon of a typical office development will already have been emitted. The figure for a residential block is 51 per cent.
The Architects Journal (AJ), the influential architect magazine, has an established campaign to promote retrofitting – RetroFirst. Launched in 2019 it calls for the reuse of existing buildings, to prioritise retrofit over demolition and rebuild, and has continued to gather much support from leading organisations and businesses in the property and construction industry.
Last summer construction giant Mace added its clout to the demand with a report recommending a ‘retrofit first’ approach to be adopted into UK planning policy. Non-domestic buildings ‘represent 13 per cent of UK building stock’, the report found, ‘but account for 23 per cent of carbon emissions from buildings, with more than 3.5 million non-residential buildings requiring retrofit in the next 10 years’.
The AJ RetroFirst campaign calls for central government to take the lead in promoting the reuse and high-quality refurbishment of all existing buildings, an even more urgent task given the new target of cutting carbon emissions by 78% by 2035. It makes three demands: for government to cut the VAT rate on refurbishment, repair and maintenance from 20% to 5% or below; to amend policy to promote the reuse of existing buildings to high standards; and thirdly to insist that all public funded projects look to retrofit solutions first.
Quality information needed
It would appear government is listening. Last summer it overturned a decision allowing Marks & Spencer to demolish and replace its flagship store on London’s Oxford Street (although subsequently lost the high court appeal), and in January this year it announced a review looking at the barriers to retrofitting historic buildings. It identified five key challenges. Chief of these was planning issues but it also found that providing better quality and easily accessible information is needed, to help historic building owners understand how to improve buildings without damaging their special qualities or fabric.
Retrofitting applies to all existing building stock but is more challenging with historic buildings because of the need to preserve their historic character which requires expensive specialist skills and materials, which are in short supply.
When you are using recycled or upcycled materials, it is highly unlikely that they will be tested to the current standards, so you have this immediate barrier"
Geoff wilkinson
According to Geoff Wilkinson, a building inspector and AJ columnist, one of the biggest challenges is that the Building Regulations are only worded to recognise the use of new materials, and these have to be certified.
“When you are using recycled or upcycled materials, it is highly unlikely that they will be tested to the current standards, so you have this immediate barrier,” he says. “What needs to happen is that the regulations are reworded and ensure that upcycled and recycled materials can be used.
“We really need to ensure that we keep much better records of products and materials that are going into buildings to ensure that the paper trail is there. BIM [building information modelling] records can help us to determine that these materials are suitable for reuse.’
In addition, Wilkinson proposes that the regs should be updated to include both an Energy Performance Certificate and a new ‘materials performance certificate’. This could ensure a whole-life carbon approach so that the embodied carbon in the materials used forms as much of a part of a building’s sustainability profile as its potential in-use energy efficiency.
This is where professional specifiers can step in with product knowledge, specifically sustainability and performance data. Using a GAI registered professional to specify architectural ironmongery in a retrofit or historic refurb scenario will result in more than merely specifying aged brass handles.
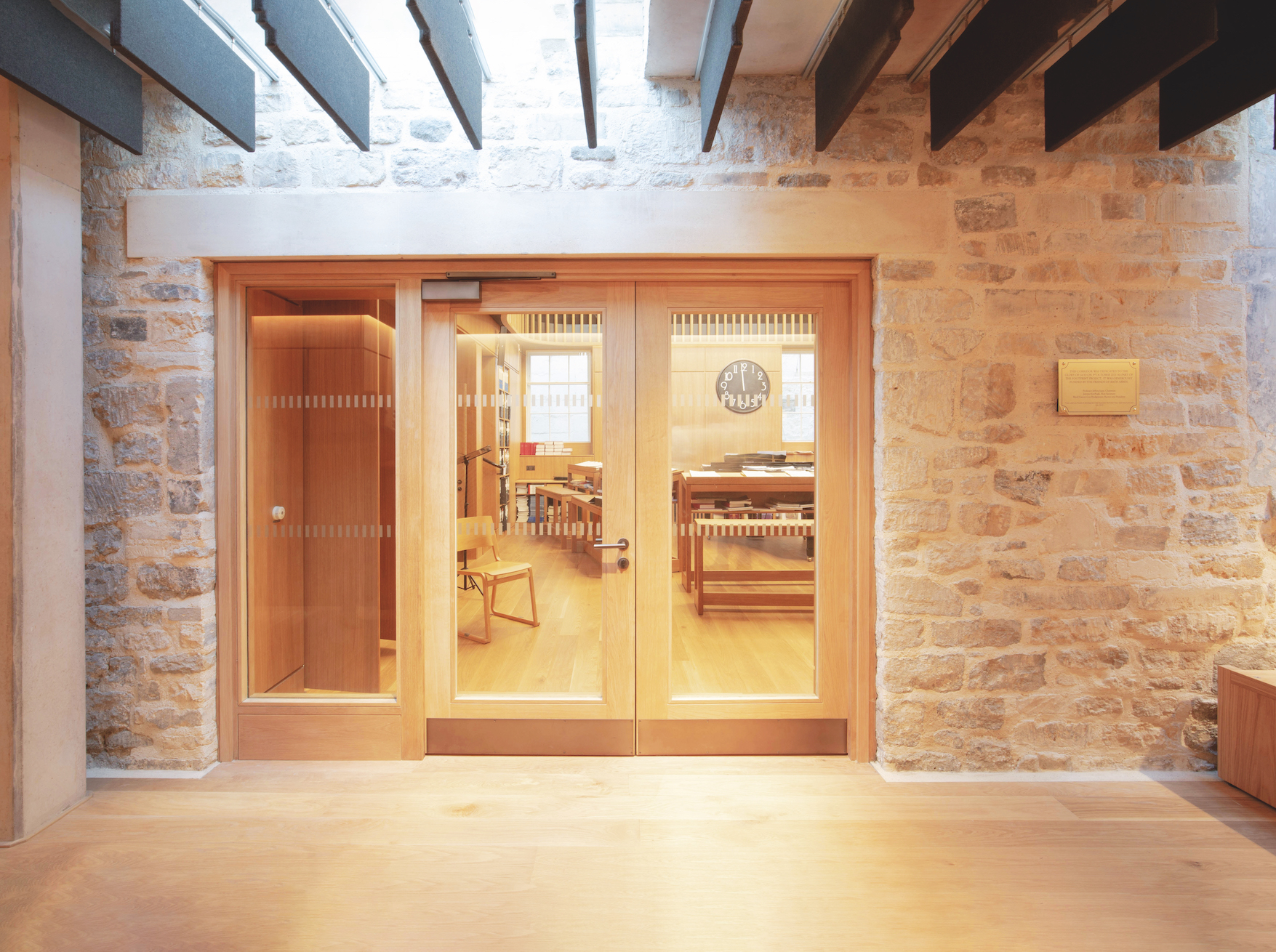
Leading by example
Brutally sensitive
Mikhail Riches won the 2023 AJ Retrofit of the Year award for its sensitive upgrade of a 1960s Brutalist housing estate in Sheffield. The light-touch approach taken included insulating the existing brickwork internally and carefully cleaning it externally. The design built on lessons from Phase 1 and on conversations with tenants, but it was also informed by observations of how the structure has been personalised by its residents. Architect Rob Wilson wrote of the scheme in the AJ: “The thorough research and deft hand that Mikhail Riches has brought to it has impressively future-proofed this listed building while remaining seamlessly in tune with the spirit of the original design. This is what retrofit is all about.”
Factory reset
Architects 5th Studio worked with social entrepreneurs Bloqs to create the UK’s first open-access factory providing maker businesses with affordable workshop space, access to state-of-the-art equipment and the opportunity to build a community of fellow makers.
The new facility is part new build and part adaptive reuse of a former vehicle testing facility. The light-filled building, eight-metres tall space went beyond preserving the embodied carbon of the original structure by not demolishing it and the whole facility is heated using waste from the timber machining workshops.
Grade 1 challenge
The Bath Abbey Footprint Project (pictured above) sought to renovate the 17th Century Grade I listed building sensitively whilst modernising its facilities to cater for present-day demands.
Allgood provided a complete package of ironmongery and a comprehensive access control solution. The project required many bespoke items to accommodate the Abbey’s historic architecture. Challenges included how to bring a 400-year-old lock back into working order as part of a modern access control systems; how to improve access control and security for the ancient catacombs which needed constant airflow to maintain the right environmental conditions; and how to supply hardware for doors and frames which were protected by Historic England listing requirements.
Competence in retrofit
Competently specifying for a retrofitting project will demand a broad knowledge of product, performance, legislation and compatibility. This would cover:
- Understanding Building Regulationsand Standards
- Compatibility and integration: is the hardware compatible with the existing infrastructure of the building?
- Security and safety: how durable is the hardware and does it meet security measures?
- Can the products improve energy efficiency, such as prevention of heat loss?
- Sustainability: what data is available for the hardware being proposed, including its environmental impact, recyclability, and use of sustainable materials?
- Warranty and maintenance: what are the whole life costs of the products?
- Compliance with historic preservation requirements: does the hardware match the original design or meet specific conservation standards?
Clever solutions
While the battle to change policy and planning continues, the architect and specifier sector is becoming increasingly inventive in its efforts to work with existing buildings and product. It’s leading to some quietly innovative interiors and clever solutions to retrofit problems.
HUT Architecture’s light-touch reworking of 210 Pentonville Road, London, for example, involved framing the entrance to be more prominent, moving, cleaning and refitting the interior’s floor tiles, and using perforated metal panels to hide older plant equipment rather than ditching it for new machinery. The approach of ‘mend and repair’ rather than ‘demolish and discard’ has led to a sensitive and detail-oriented design that might not have emerged if building from scratch.
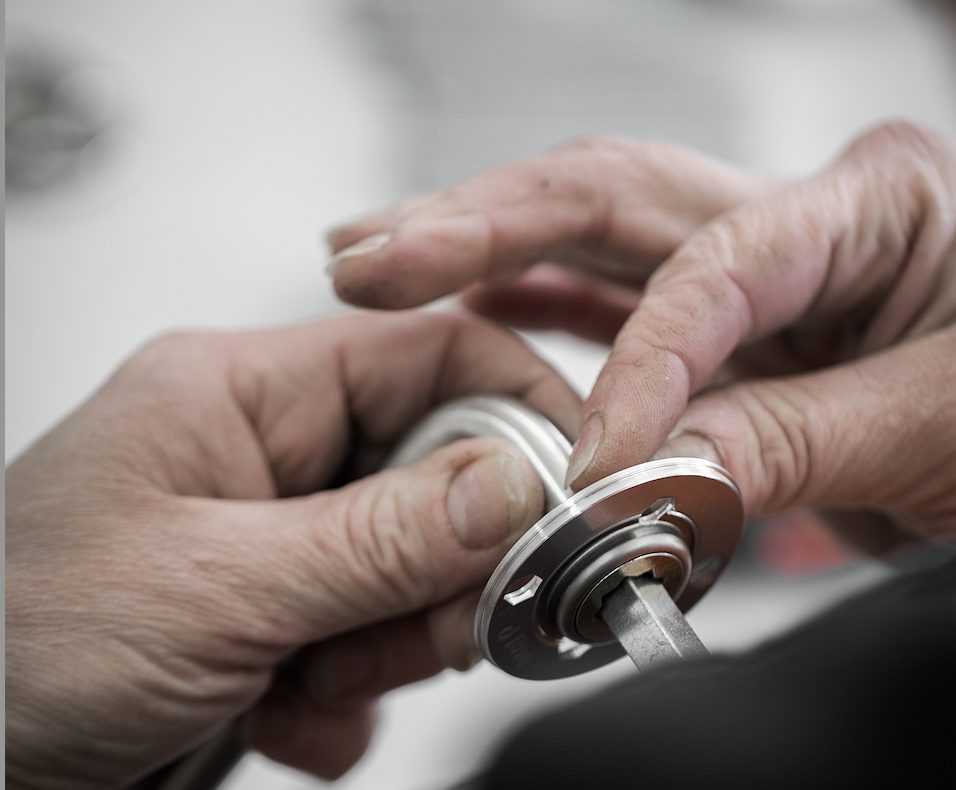
This philosophy has also been seen with dline’s Rehandle initiative, the industry’s first circular economy offer. The Danish door hardware designer takes original products to be fixed, parts replaced and brushed to work as good as new. The firm claims each Re-handle® will save up to 90 per cent CO2 emission and claims to prolong the life of products up to 100 years. dline is challenging the industry to Re-handle® the same product up to four times. “With each Re-handle® the 20-year product warranty period is renewed, securing 100 years of use. With an asking price for a Re-handled product that is 60% lower than a newly produced item, it is straightforward to make the enduring choice and reuse instead of buying new.
“Based on the fact that every new product put into the world has severe CO2 impacts, choosing to Re-handle® products instead of producing new will dramatically reduce its carbon footprint between 54-91%, depending on the product,” the firm claims. dline has documented its products’ complete Global Warming Potential (CO2emission) across the entire life cycle, based on fully documented, internationally recognised EPDs.
In a seminar held at Architect@work event in March, titled ‘Re-use and Regain’ a panel of experts debated the retrofit issues and posed a provocative question: given that most of the buildings that will be standing in 50 years time have already been built, how can we adapt structures in creative and exciting ways to inspire the next generation to consider whether we should be building at all?