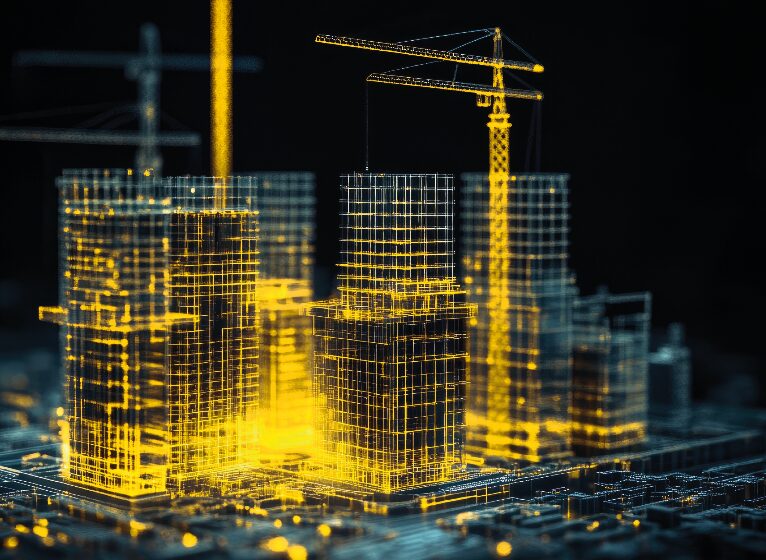
Following Construction Leadership Council (CLC) research that shows a widespread lack of understanding within the manufacturing industry over the nature of keeping a digital record, AIJ provides the lowdown on this way of working
The term ‘golden thread’ came into existence in 2018 in the Building a Safer Future report, commissioned by Dame Judith Hackitt. Noting that existing building and fire safety regulations and processes for constructing high-rise buildings were “not fit for purpose” the report called for a move towards digitisation of product information and effective, accurate storage and management of information concerning buildings’ designs, construction, and uses. This was dubbed ‘the golden thread’.
Specifically it refers to a robust and traceable flow of information that connects everyone involved in a building’s lifecycle – from design, construction, and installation to occupation, maintenance, and eventual demolition. It ensures that accurate information about materials, processes, and decisions is not only recorded but also accessible to everyone who needs it.
Why is it important? For a few reasons:
- Building trust and confidence
Safety is a cornerstone of the construction industry. The golden thread helps ensure that buildings are constructed and maintained with the highest levels of safety in mind. By having a clear record of materials used, methods employed, and decisions made, stakeholders – including clients, contractors, suppliers, and end-users – can have confidence that every step has been documented and can be verified.
- Ensuring compliance and regulation
The golden thread ensures that regulations are followed, from product specification to installation, and provides a foundation for verifying compliance long after construction is complete. This transparency can help organisations avoid costly fines, legal disputes, and brand damage.
- Improving efficiency and reducing waste
Inaccurate or incomplete information leads to costly mistakes, unnecessary waste, and delayed projects. The golden thread promotes efficiency by providing all parties with the right information at the right time, reducing the chances of rework and miscommunication.
- Driving innovation in product development
With detailed information about how materials are used in the field, manufacturers can gain insights that drive innovation in product development. Feedback from installation and maintenance teams can identify potential areas for improvement, enabling companies to refine their offerings, design safer and more durable products, and ultimately contribute to a safer built environment.
- Enhancing accountability across the supply chain
One of the golden thread’s most valuable contributions is the level of accountability it brings across the construction ecosystem. From the architect who specifies materials to the installer who fits them and the building manager who oversees the completed project, each person is accountable for the decisions they make.
The problem is
Six years on from the Building Safety Report however and problems remain. Recent research by the Construction Leadership Council (CLC) has shown a widespread lack of understanding within the manufacturing industry over the nature of keeping a digital record and how it could be achieved.
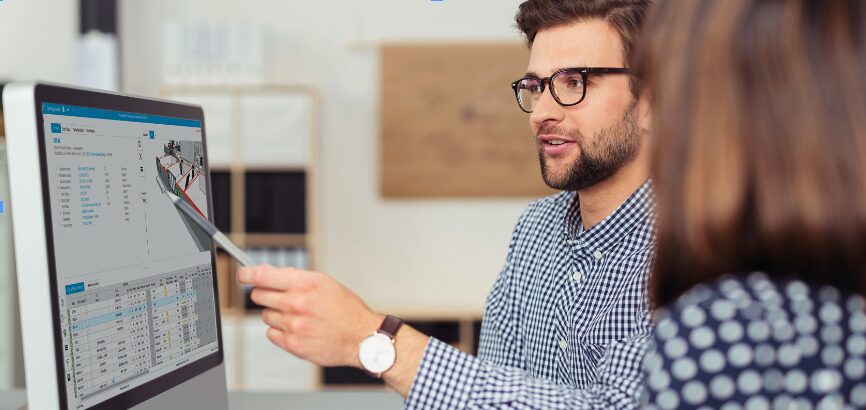
In fact, 92% of product manufacturers do not see digitisation as a major concern and more than half “see no need to digitise”. 85% of companies still provide product information largely via pdf or hard copy only and only 8% have ever made or commissioned a Building Information Modelling (BIM) object. Just over half of respondents felt they were digitised to some extent, but even when provided with the definition of digitisation, few of the respondents fully grasped and understood what it meant in practice.
Even among those who consider themselves partially digitised, there is often a fundamental misunderstanding of what true digitisation is. Many equated digitisation with using computers or having online systems, rather than understanding it as a comprehensive approach to maintaining and integrating critical safety information throughout a building’s lifecycle.
Nicola John, managing director of Fire Door Maintenance, part of UAP Ltd, says businesses must treat the golden thread as more than just a record-keeping tool. “It is a framework for linking different parties within the construction industry,” she says. “By connecting architects, engineers, contractors, manufacturers, and building owners, the golden thread fosters transparency and collaboration.”
Embracing the golden thread requires a shift toward adopting digital technologies and robust data management systems. Here are some key steps:
- Adopt digital documentation systems
Ensure that data related to products is available in digital formats that can be easily accessed and shared. Cloud-based platforms and digital twins are examples of tools that can make data available throughout the building’s lifecycle.
- Invest in data training. Employees must be trained to understand and manage data responsibly. Properly recorded and maintained data forms the foundation of the golden thread, and training ensures everyone understands its value.
- Engage with supply chain partners
Collaboration with supply chain partners ensures that product data remains consistent and traceable from manufacturing to installation.
- Standardise product information
Clear, standardised product information supports compliance and ensures all parties have a common understanding of the materials in use.
Head in the game
Some members of the architectural ironmongery industry are already on board with digital technology that enables the golden thread. ASSA ABLOY for example, has asset tagging functionality of its Openings Studio BIM software solution.
Openings Studio is a cloud based, custom configuration tool for the creation, visualisation, modification, and management of door openings. It is uniquely integrated with the building model as part of a live and dynamic environment. Every door logged in Openings Studio is automatically assigned a unique asset tag, which can be affixed to the door as either a QR code or RFID Tag, enabling direct access to the door details, including installation, inspection, and service history.
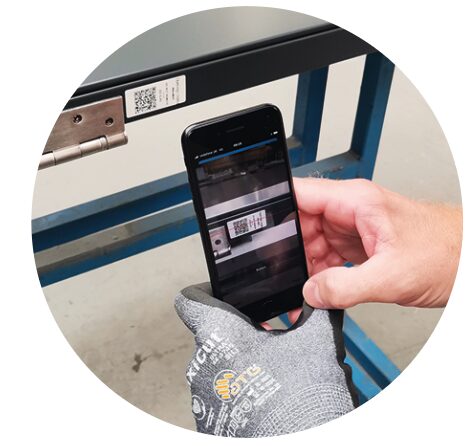
The asset tag functionality enables direct access from the mobile app to data such as product specification, hardware schedule, product information, inspection reports, digital images, and change management tracking.
Brian Sofley, managing director at ASSA ABLOY Opening Solutions UK & Ireland Door Group explains: “Our RFID asset tagging system is uniquely creating that ‘golden thread’ of information, enabling direct access to door details, including installation, inspection, and service history. Ultimately, this provides a holistic approach and ensures accountability across the board.”
Openings Studio™ Building Information Modelling (BIM) Software provides access to complete doorset information at all stages from product concept to product care. The Openings Studio Mobile App allows users to manage buildings as a holistic system, and design, build and maintain openings for their entire lifecycle.
Information stored within the app enables buildings to be safely and effectively designed, constructed and operated, providing a seamless link between design intent during the specification process onto the product in service.
Philip Duckworth, chairman of FireDNA says digital asset tracking and monitoring using QR Codes and RFID Tags has been around for many years but says that recent advances in cloud computing and mobile device technology means “we are now able to do more than we ever could, in a faster, more interactive, robust and secure way”.
FireDNA is a cloud-based software and a mobile App specifically designed for passive fire products. Developed alongside product manufacturers, installation contractors, fire door and passive fire product inspectors, building owners and their maintenance teams, FireDNA links everyone in the ‘chain of responsibility’ across the full lifecycle of a product from cradle to grave, delivering a ‘golden thread’ of fire safety information.
“Our system catalogues manufacturers’ product data, including ironmongery specifications and digitally shares it with contractors and installers, who in turn add their installation data, that can then be passed on to building owners, FMs and TMO’s,” Duckworth explains.
“FireDNA is a digital conduit that enables the upload, collation and access of critical fire safety information; certification, technical data sheets and remediation and maintenance guides ‘at the point of need’.
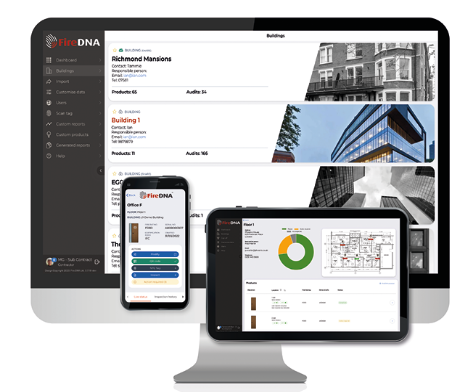
It provides time and date stamped evidence of not only the products manufactured and specified, but also details installation and maintenance activities and competencies, which ultimately delivers complete digital compliance in-line with the ‘golden thread’ principles,” says Duckworth.
Access to the FireDNA Software and Mobile App can be shared with building control, fire safety officers and insurers. FireDNA has also developed a free app for tenants and residents, enabling them to see if their buildings passive fire products are safe, when they were last inspected, by whom, and when the next inspection is due. They can also see their own maintenance responsibilities relating to their fire rated flat entrance door.
Challenges persist
Despite some key players on board with golden thread Nicola John says there is still a way to go. “It’s clear the industry is still not meeting post-Grenfell regulatory requirements to digitise product information, and widespread training to understand the golden thread is needed before we can put it into practice,” she says. “Manufacturers, installers, inspectors, and landlords often work in isolation, focusing solely on their tasks without considering the broader impact on other stages of the building lifecycle.
It’s clear the industry is still not meeting post-Grenfell regulatory requirements to digitise product information, and widespread training to understand the golden thread is needed before we can put it into practice
Nicola Johns
“This disconnection causes a lack of communication and oversight, with no ‘golden thread’ to link all product information throughout construction. Without accessible product data, critical safety issues can remain hidden. The consequences of siloed practices have been fatal. The Grenfell disaster was a stark reminder of this danger.”
And while technological advances now make it easier to maintain the golden thread of information John says digitisation alone isn’t enough. She argues that education on understanding the entire lifecycle of safety products is essential.
Fire Door Maintenance, part of UAP, is training the industry to bridge this knowledge gap. “It’s the UK’s first practical fire door training centre, covering everything from regulation compliance to how and why components were chosen in product engineering and how products are ultimately installed for the end user,” she says.
Those who embrace the golden thread will find themselves better prepared for future compliance requirements and industry shifts; a strategic move that can set them apart in an increasingly competitive market. But more crucially is not losing sight of why the golden thread needed to happen. As John puts it: “By maintaining a comprehensive and integrated digital record, the golden thread helps ensure that safety remains at the forefront of every stage of a building’s life, protecting both the structure and its occupants.”