CPD
Intumescent products are often hidden from view but are a vital part of the construction of a fire rated doorset. Dave Boulton and Russell Smith explain the applications and characteristics of these key products.
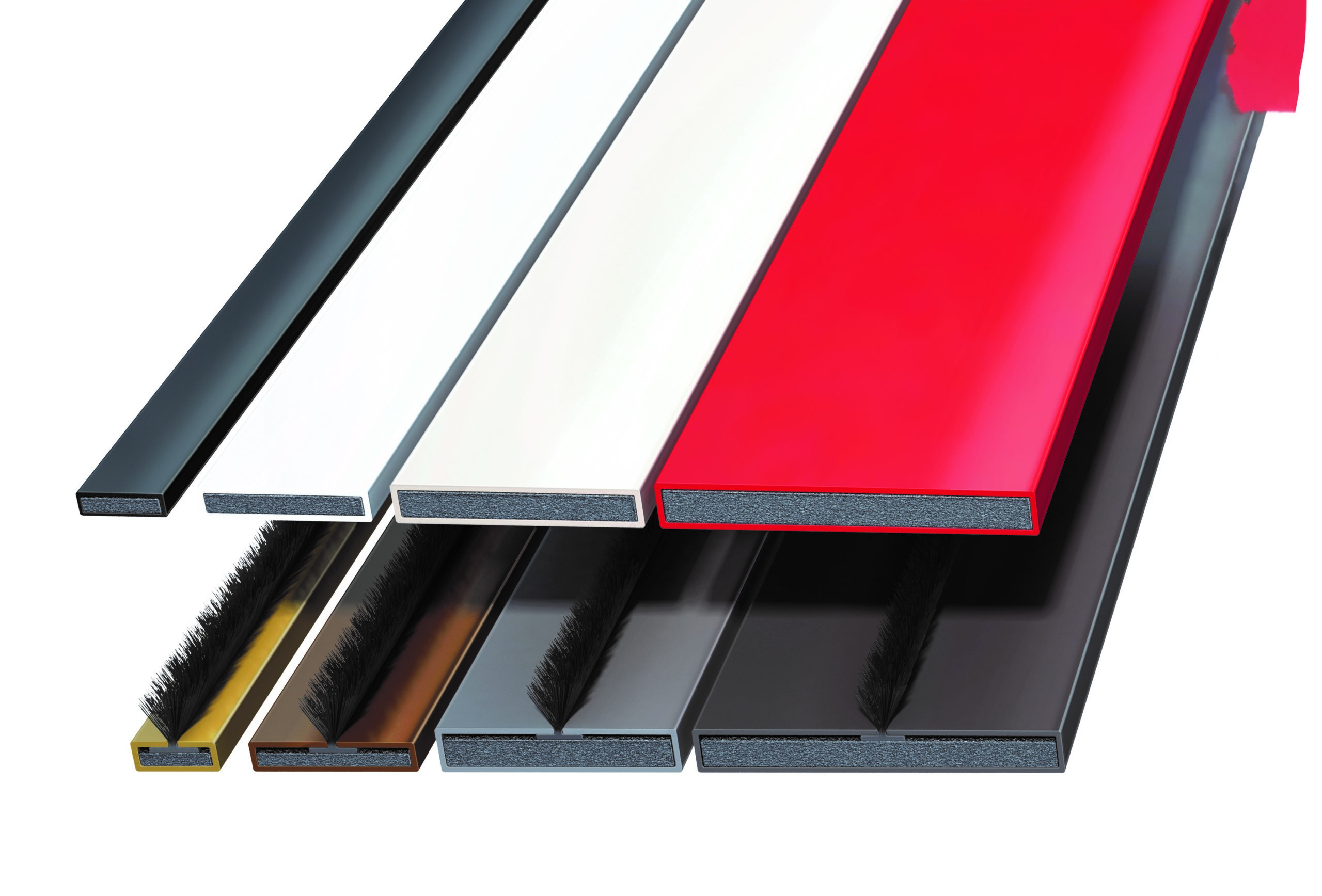
To the casual onlooker, a fire door is a fire door. Not much thought is given to the parts you cannot see with the naked eye, however intumescent seals and gaskets make a significant contribution to the performance of a fire rated door set. It must be emphasised that the correct intumescent as recorded within the test report is used in the intended assembly.
Before looking at where intumescent products fit on a fire door, first a brief overview of the materials themselves, and three main intumescent types: Mono Ammonium Phosphate (MAP), Hydrated Sodium Silicate and Intercollated Graphite. Intumescents are also categorised as non/low pressure generating and pressure generating. It is important to realise the difference between the two categories as using the wrong type in the wrong location can and will have a dramatic effect on the intended fire performance of the system it is used in.
Mono Ammonium Phosphate (M.A.P)
MAP is commonly used under and around ironmongery items as well as in fire rated glazing applications. MAP is categorised as a non-pressure generating intumescent and will produce high levels of expansion when activated at around 180°c. Depending on the thickness used it can exhibit an expansion of up to 40 times its original thickness and, as the expanded char exhibits no significant pressure, the material will have a minimal impact on the item it is designed to protect.
Hydrated Sodium Silicate
This is typically used as door edge seals for both timber and steel applications as well as glazing and ventilation grilles. Silicates are often encased in PVC sleeves as the product has limited protection against atmospheric moisture. It is categorised as a pressure generating intumescent and will produce a level of expansion of up to 12 times its original thickness. The expanded char is rigid in structure and it is this rigidity that provides the pressure generating characteristic of this intumescent type. Expansion starts around 100°C when steam blisters are formed by evaporating water contained within the product which, when released as part of the expansion phase, can have the added benefit of cooling the area around its location.
Intercollated graphite
Typically used as door edge seals for both timber and steel applications as well as glazing, pipes and cable penetrations. Intercollated graphite is manufactured by many different organisations and depending on the formulation of the product can provide low through to high pressure generating capabilities. Typical expansion ratios can be up to 25 times its original thickness. The expanded char is unique in as far as each flake of graphite when heated will react in a corkscrew manner and as the individual expanded flakes interlock the structure is formed. Expansion starts from around 180°C through to 250°C. Graphite has the ability to re-expand if movement within the sample occurs or if part of the expanded char falls away as a result of erosion or movement. Graphites are generally suited to high moisture
and external environments and are
often used in offshore applications.
Application
- Hardware protection
Hardware protection kits are manufactured from MAP material, and precision cut on CNC machines to suit any lock, hinge or door closer detail.
The requirement for ironmongery protection kits will form part of the fire test evidence of either the hardware manufacturer or the door set manufacturer. They will be key to maintaining the integrity of the door in a fire situation. It is imperative that the correct material, material thickness and kit design is used to ensure compliance, as incorrect specification could have a detrimental effect on the fire door integrity.
- Fire rated Air Transfer Grilles
Where there is a need for air transfer through a fire door the integrity of the door must be maintained. Fire rated air transfer grilles manufactured from Hydrated Sodium Silicate or graphite offer the solution. Slim in design they allow ease of installation and can be supplied with decorative cover grilles of various designs. Fire test evidence of size and location should be examined to ensure they meet the requirements of the application, e.g. low or high level. Also, fire door test evidence should be reviewed to ensure the fire door has been tested with an aperture of the required size and location.
- Glazing
Glazed apertures are an important part of a building. When required in a fire resistant door or fire compartment wall they must be a fully tested system, of glass, bead and intumescent seal. There are various products available which include channel systems, PVC encapsulated systems, which offer flexibility in colour finish and single strip systems. Timber bead detail is also important and fire test evidence should be viewed to ensure correct design detail, fixing detail and material; e.g. softwood or hardwood.
- Threshold seals
The threshold of a door is often forgotten about but fire, smoke and acoustic requirements must be considered. Cool smoke is less buoyant and therefore not protecting the gap at the bottom of a fire and smoke door could allow potentially harmful gases to pass under it. The use of an automatic threshold seal (where the seal lifts when the door is opened) offers an ideal solution to this problem. These products can be face fixed or rebated into the bottom of the door. Fire test evidence should be reviewed to ensure when fitting to a fire door, as there may be a need for an intumescent kit of some kind to meet the fire test evidence. These products by their very nature also offer acoustic sealing properties.
- Fire and cold smoke seals
The fire seal forms part of the fire test evidence of the door so the correct seal size and intumescent material used must be adhered to. Different intumescent materials should not be used around the door perimeter as this could have an adverse effect on the door in a fire situation. As well as being the ‘seal’ between door leaf and frame, in a fire situation, for ‘S’ rated doors (require cold smoke protection) the seals would have a brush or fin detail. These ensure that there is a seal between the leaf and frame before the heat activates the intumescent, thereby prohibiting the passage of cold smoke around the perimeter. As a retrofit product, assuming the intumescent seals are in good condition, a finned perimeter seal, that is fitted in against the door stop can be used.
- The importance of testing
It is essential that the correct intumescent as recorded within the test report is used in the intended assembly. Manufacturers spend a significant amount of a research and development budget on fire testing and often assemblies have to be re-tested to get the desired result. Not only is the correct type of intumescent required it should also be matched to the manufacturers actual brand used in the original fire test. Only then can you be certain that any potential intumescent variation has been removed. Controlled substitution of intumescent materials is possible under third party approved certification schemes.
As always, the test evidence or certification should be studied and understood before selecting an intumescent product.
Dave Boulton is commercial director and Russell Smith is technical manager at Mann McGowan.