Henry Rowden, technical manager at Vanquish Hardware Protection, examines critical responsibility gaps in fire door intumescent protection specification and supply chains
It is widely understood within the fire doorset and fire door hardware industry that intumescent hardware protection plays a crucial role in fire-resistant doors. When fire doors are rebated to accommodate locks, latches, concealed door closers, flush bolts and the like, the door’s integrity can be compromised.
Intumescent materials help maintain the structural integrity of the door during a fire by filling any gaps created during the rebating process, thereby resisting the passage of hot gases and flames around weak points in the door.
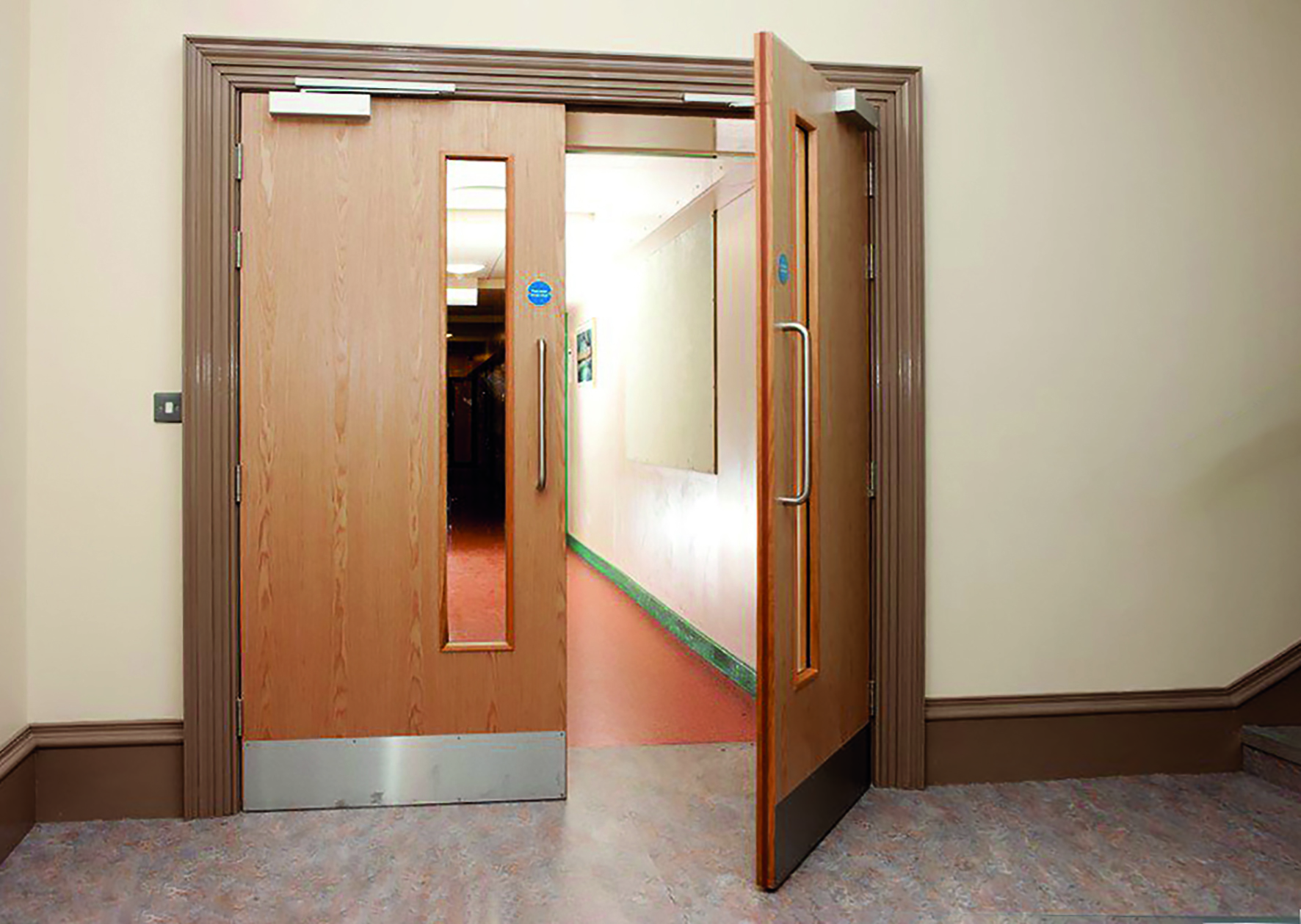
But, we are seeing that greater clarity is still needed around who holds the responsibility for ensuring the correct intumescent protection is installed/specified, and whether that individual has access to all the necessary information.
Many hardware manufacturers sell their products without including intumescent protection, citing the valid point that they cannot always determine whether the hardware will be fitted to a fire door or a standard internal door. While understandable, this approach can inadvertently contribute to confusion and challenges further along the supply chain.
It is often the case that installers of fire doors, locks, hinges, and other hardware may not have access to supporting evidence for a particular door configuration. Additionally, many products on the market are not covered by third-party certification schemes like Certifire, making relevant test information difficult to obtain and rarely available on manufacturers’ websites.
As manufacturers of intumescent products, we frequently receive inquiries from installers unsure whether intumescent protection is required, and we learn that the relevant hardware manufacturer does not supply a suitable intumescent kit. This situation is concerning.
When a manufacturer undertakes testing to bring a product to market, whether according to BS476:22 or more commonly BS EN 1634-1, they must ensure that end users have the information necessary to fit the hardware to a fire door in accordance with its supporting evidence, including using the correct intumescent materials — this enables traceable, evidence-based decisions and consistent application aligned with the product’s tested performance. Not all intumescent products perform equally, for example, and even minor changes in specifications can significantly impact the integrity of a fire-resistant door.
I recently spoke with Bryony Matthews of Iron Out, an independent ironmongery consultant, whose impartial consultancy work spans competence, compliance, and quality assurance, to gain her perspective on current industry challenges.
Matthews said: “The demand for clarity is increasing, and we’re seeing the industry collaborate in new and more effective ways to raise awareness, so that end users can be more confident about safety.
“I empathise with manufacturers. They often have limited or unclear information about where their products are going or how they’ll be used, which can make it incredibly difficult to ensure they’re being specified, installed, used, and maintained correctly, let alone have the means to justify investing in further development like performance testing.
“In some cases, when a manufacturer asks questions to better support the customer, the customer may be reluctant to share details, whether out of fear they’ll lose the job, or fear the manufacturer will supply direct.”
Reflecting on broader industry changes, Matthews added: “With the emphasis on the Golden Thread, traceability, and anticipated change around how construction product information is shared, many suppliers are rightly investing in this area. Some are already doing exciting things with tech. As visibility increases and buyers become more informed, it will be interesting to see how the competitive landscape evolves.”
Matthews’s comments highlight how, post-Grenfell, the construction industry has had an increased emphasis on compliance, traceability, and third-party certification. Despite this shift, some manufacturers and suppliers hesitate to provide safety-critical intumescent protection alongside their hardware, often due to the reasons discussed, including concerns about price competition or because their testing is limited to specific applications. This leaves customers responsible for ensuring compatibility in their chosen configurations.
While the door manufacturer’s test evidence, or Field of Application, remains the gold standard for specifying the correct products, these documents are extensive and complex, often spanning hundreds of pages. Not every item of rebated hardware will be listed in one, and updates occur only every few years. As a result, newly introduced products, such as smart access control devices, may not yet be included. This places the burden on specifiers to verify proper testing and the use of the correct intumescent protection. If the hardware manufacturer does not supply an intumescent kit, it is unlikely the hardware will be installed as tested.
This challenge is echoed throughout the supply chain. For example, many architectural ironmongers and distributors stock a wide range of hardware suitable for fire doors, usually noted in the product description, however, it is less common for the required intumescent kits to be listed alongside the hardware. At best, there may be a note such as ‘lock must be fitted with required intumescent jacket if fitted to a fire door if applicable.’ Unfortunately, this level of information is insufficient for installers or specifiers to guarantee compliance. Commercially and practically, it benefits all parties to make appropriate intumescent protection accessible alongside fire-rated hardware, whether through supply, clear specification, or supporting documentation. While the consumer ultimately bears the cost, the value of life safety is immeasurable.
Through our work with manufacturers, installers, and distributors, it is evident that the knowledge gap surrounding intumescent hardware protection remains significant. Vanquish is helping address this through CPD presentations on hardware protection and fire doors via the GAI. However, greater effort is needed from manufacturers and distributors to support end users in meeting compliance requirements. This is not just a regulatory matter, it is essential to safeguarding both property and lives.