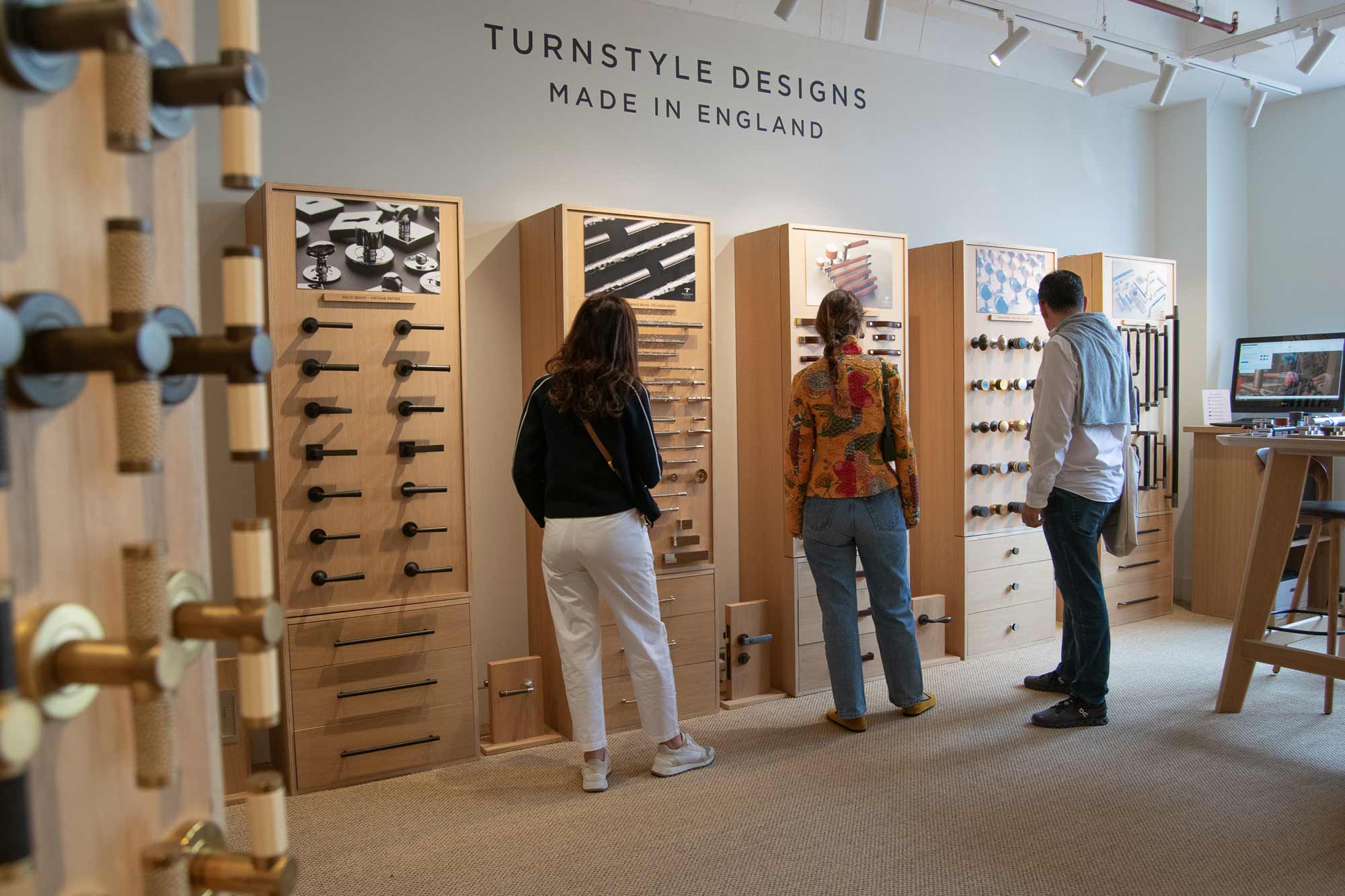
Turnstyle Designs, artisans of unique, handmade hardware, has become the first manufacturer in the sector globally to become B Corp certified. Sustainability and community has always been a key value of the Devon-based business, and this is a significant milestone for a brand that aspires to lead and inspire other businesses to follow suit.
The process took into account their exemplary staff care and strict guidelines on material sourcing, product creation, packaging and waste, and the eco-friendly facilities. The company secured a B Corp score of 99.1 out of 200 possible points. A score of 80 is required to qualify, which most brands do not meet on first attempt, and 50 the median secured by brands in the process.
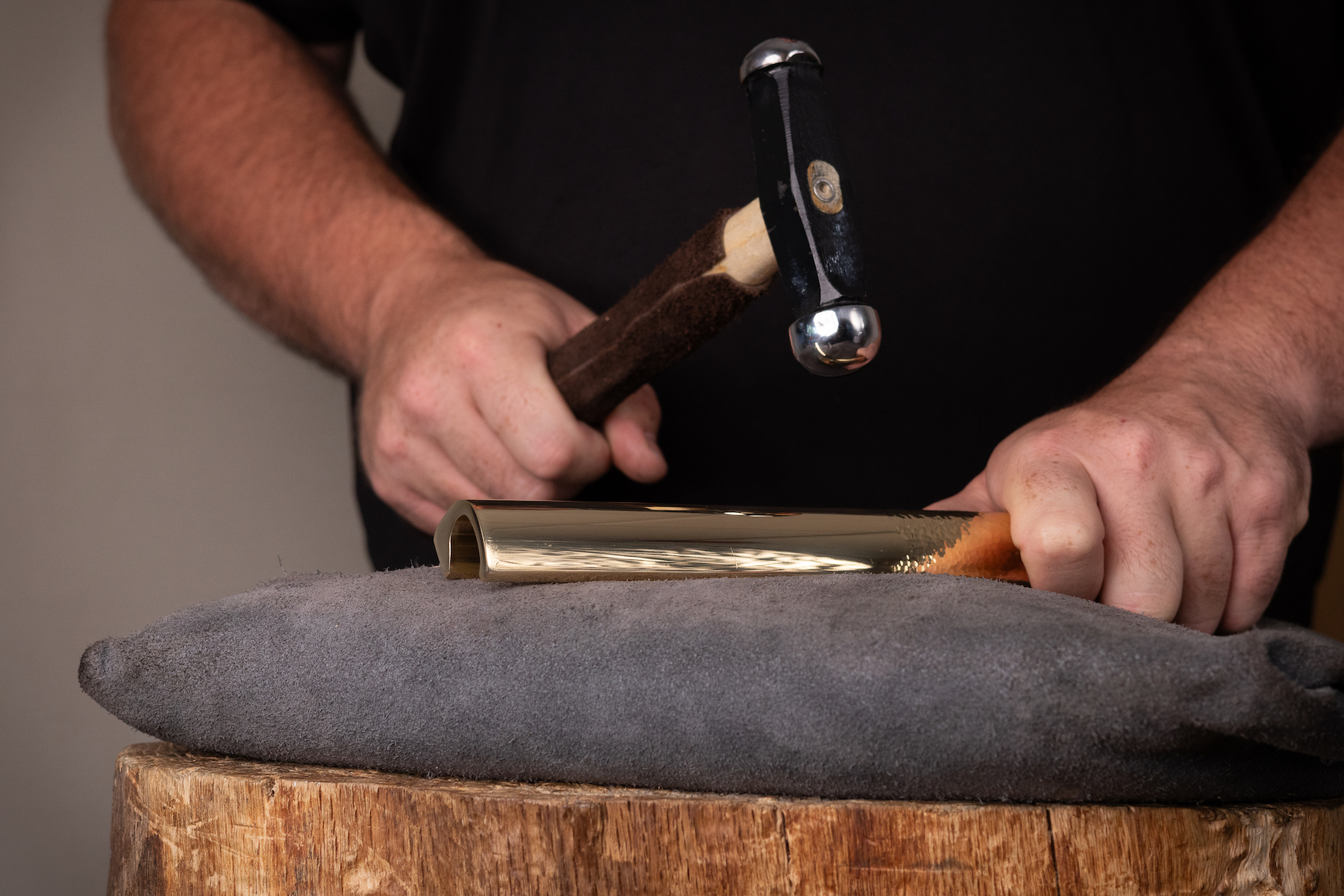
Speaking on the achievement, managing director Oscar Roberts commented: “Becoming a B Corp is one of the most important achievements in our company’s history. Since first discussing certification in 2022 this has been firmly in our sights as a target for the business, stemming from a belief that putting people and the planet first is paramount. It was an incredibly rigorous process andshone a light on our successes, as well as the work that still needs to be undertaken. The truth is we have operated in this way for several years but being able to have it externally recognised by a leading organisation like B Corp was an important step towards cementing these values into the company’s fabric. I take great pride in everyone at Turnstyle’s attitude towards being a responsible company.”
From garden shed to super yachts
Started by Steve Roberts in a workshop at the foot of the Roberts’ family garden, Turnstyle Designs has grown into an award-winning, globally-renowned business, operating out of purpose-built factory and offices in beautiful North Devon, England. Over 30 years on, now employing 55 staff, they are one of the foremost producers of luxury, design-led hardware in the world, supplying some of the most prestigious and interesting building and super yacht projects in over 50 countries worldwide.
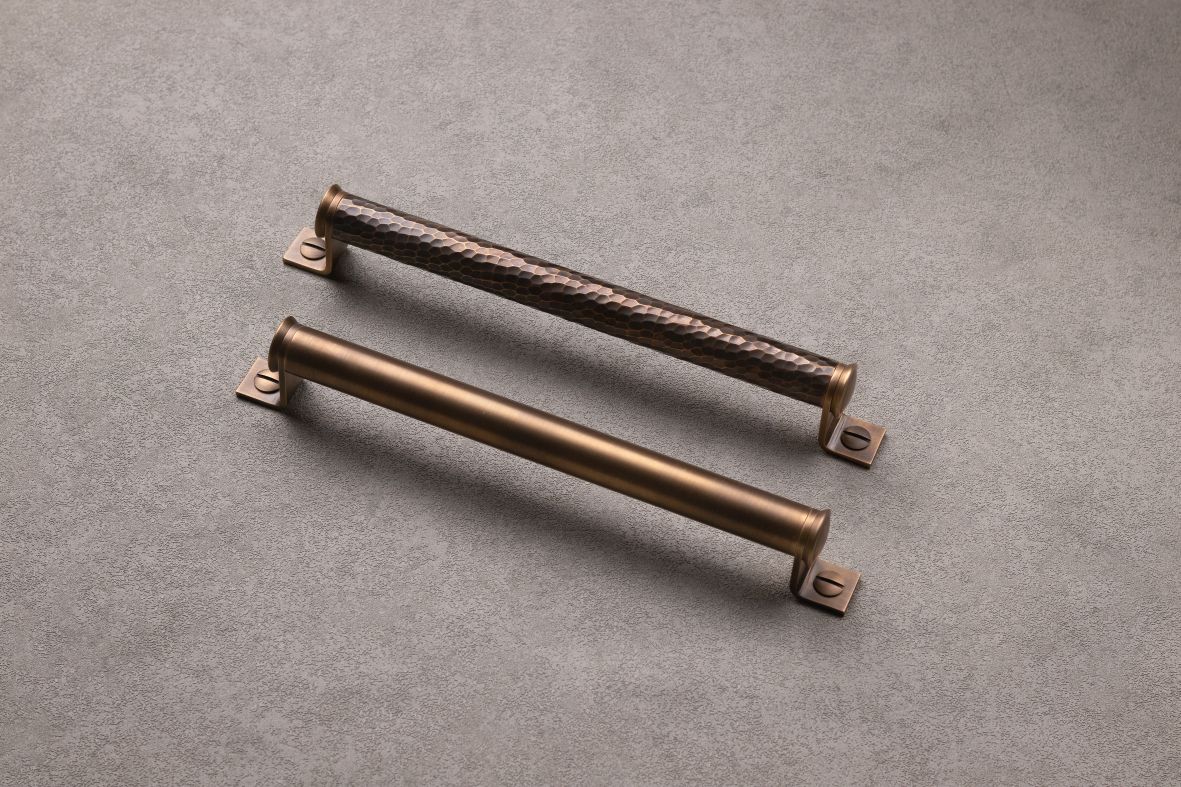
The brand’s commitment to driving change in the industry has been a priority for a number of years across all areas of the business from manufacturing, product, and wider business evolution. Turnstyle Designs’s founder, Steve Roberts, was quoted in 2019 stating: “all the evidence for climate change is too powerful and present to deny, so we have two choices, do nothing and bury our heads in the sand, or act and act now. Businesses, regardless of size all have a responsibility to push sustainability to the front of their agenda. Economic and ecological sustainability are intrinsically linked, you cannot be one without doing the other.”
Turnstyle’s initiatives for people and the planet include:
Support, restore and improve: flagship charity program, as member of 1% For The Planet since 2020, it now donate at least 2% of annual turnover to local environmental and social charities. 100 hours of staff volunteer work organised throughout 2024. The initiative focuses on the North Devon area and working with local charities to support the community and environment.
Materials: leathers are sourced from European farms and tanned used natural vegetable dyes. The hides are byproducts from the meat industry. Trademark Amalfine material is created using 80%byproducts from other manufacturing processes, such as marble and bronze dust.
Factory: 100% powered by renewable energy, with over 50% derived from PV solar panels on theroof of the facility. No single use plastic in the production process, and certified zero to landfill policy since 2019. It is in the process of building a new factory which will meet the highest sustainability standards while also improving the work life of all staff at their HQ.
Packaging: cardboard made from recycled paper, and printed with water based inks – the end result is fully recyclable. 100% of plastic has been removed and replaced with biodegradable or recyclable alternatives.
Circular economy: products can be sent back to the factory for repairs. Items beyond repair arereturned, broken down, and each element recycled.
Employees: cycle to work scheme begun in 2019 to encourage sustainable travel to and from theoffice. Company cars are electric if required for external meetings (most are virtual).
Carbon offsetting: every element of output is measured. Certified carbon neutral since 2020.
The team understands that there are additional challenges to face moving forward and continues to strive for innovative ways to improve the relationship between humanity and nature further. It is constantly researching new material possibilities and formations, principally to decrease the resin required in its trademark Amalfine (currently 15-20% of the material makeup). Increasing its work with local partners, one of the main aims for 2025 is to encourage greater awareness of blue farming and the responsible growth and harvesting of seaweed. Hoping to begin with a local primary school will inspire the younger generation to engage with sustainable materiality from an early age. In addition to mitigating its carbon output, the team aims to offset additional carbon in the local area by planting trees and creating green spaces for the community to enjoy.
For more information see Turnstyle’s Impact Report https://www.turnstyledesigns.com/app/uploads/2024/12/Impact-Report-2024-Turnstyle-Designs-Reduced.pdf